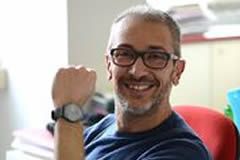
PUPA è un’azienda che da 30 anni realizza e distribuisce prodotti cosmetici in Italia e in 67 Paesi del mondo, promuovendo i valori del “made in Italy". In Italia la sua rete di distribuzione comprende circa 5.000 profumerie, mentre in Europa è presente in Francia, Austria, Romania, Slovacchia, Ungheria e Repubblica Ceca. Abbiamo intervistato il suo logistics manager, Marcello Di Francescantonio, di recente intervenuto alla cerimonia de "Il Logistico dell'Anno 2017", che ha visto assegnare proprio a PUPA una menzione speciale per il progetto "Gestione innovativa del processo di resi" realizzato con KFI, system Integrator specializzato nell’implementazione di progetti innovativi per l’efficientamento dei processi lungo tutte le fasi della supply chain.
Frammentazione, capillarità del delivery e tracciabilità dei lotti sono sempre più fattori chiave per il successo di un’azienda. Come sta affrontando PUPA tutto questo?
La distribuzione di PUPA deve affrontare ogni giorno esigenze che vanno dalla consegna del singolo pezzo in profumeria fino a pallet mono-referenza nelle catene organizzate e nei grandi distributori esteri, senza dimenticare l’ottimizzazione dei costi. La nostra missione logistica è rivolta allo studio di strumenti e innovazioni di processo, talvolta mutuati anche da esperienze logistiche in altri settori: la tracciabilità dei lotti e la movimentazione mediante prepack multi-codice/colore sono solo un paio di esempi di come esperienze importate dal mondo del fashion e della GDO abbiano consentito il raggiungimento della qualità e della sostenibilità economica lungo tutta la nostra filiera. Il recente progetto dei resi è un altro esempio di come un processo di pick to light usato al contrario possa consentire forti efficienze anche nella reverse logistics.
Di recente avete ottenuto, assieme a KFI, la menzione speciale al premio Il Logistico dell’Anno 2017 per il progetto di gestione innovativa del processo di resi: cosa vi ha spinto a intraprendere questa soluzione?
Da anni la nostra azienda ha scoperto la
strategicità e la sostenibilità che si celano dietro alla gestione dei resi.
Mancava l’ottimizzazione che consentisse di aggiungere efficienza a un
processo già consolidato, permettendo l’ottenimento di nuove sinergie lungo
tutta la supply-chain: velocità nell’emissione delle note di credito verso i
clienti, riduzione delle differenze inventariali, ricondizionamento dei
prodotti in logica di "flusso teso"
Vogliamo approfondire le caratteristiche della soluzione che PUPA ha realizzato col supporto di KFI?
In collaborazione con KFI è stato studiato un processo di sorting in grado di combinare sia la necessità di identificare con efficacia i prodotti restituiti dai punti vendita, sia di garantire una gestione efficiente del processo di reso e di ricondizionamento per destinare con rapidità i prodotti al canale outlet. Sono state progettate delle postazioni basate sulla logica di ventilazione multireferenza vs monoreferenza, combinando le tecnologie put to light e barcode con un software progettato su misura che permette di scegliere la modalità di sorting a seconda della tipologia di ordine di reso, nonché di lavorare ordini più voluminosi o identificare in tempo reale quali prodotti risultano essere fuori gamma e quindi non ricondizionabili. Il funzionamento della soluzione è molto intuitivo e grazie all’ergonomicità delle postazioni rende il processo rapido ed efficiente: i colli in ingresso vengono aperti e i prodotti scannerizzati. Lo scanner invia un segnale che si traduce in un impulso luminoso in corrispondenza di uno dei molti vassoi presenti su una rastrelliera creata appositamente per Pupa. L’operatore può dunque collocare il prodotto nel posto giusto con la certezza automatica di aver suddiviso tutti prodotti in maniera veloce, precisa e senza sprechi. I singoli vassoi sono inoltre già pronti per essere confezionati, garantendo quindi una messa a stock univoca. Oltre alla praticità, un ulteriore punto di forza della soluzione è la flessibilità del software messo a punto da KFI. Dopo la verifica del contenuto del collo, infatti il software è in grado di compiere un’analisi qualitativa e quantitativa e proporre le diverse opzioni di sorting che possono essere funzionali per il reso. Terminata la fase di sorting permette non solo di mettere a stock la merce, ma anche di collegarsi direttamente con il sistema gestionale per l’interscambio di dati: in questo modo tutta l’azienda ha visibilità immediata della disponibilità fisica di ciascuna referenza permettendo di attivare il processo di rimessa a mercato dei prodotti rientrati verso gli outlet.
Di quale aspetto del progetto andate più fieri?
La nostra è un’azienda creativa: la logistica stessa è spesso
frutto di creatività e idee attraverso le quali è possibile "liberare"